Posted March 22, 2018
Engineers find unusual inspiration for 3-D printed surgical needle design
The needles, designed by Associate Professor of Mechanical Engineering Parsaoran Hutapea and PhD candidate Mohammad Sahlabadi, are on display at the Franklin Institute.
Video Production:
Gina Benigno and Louis Peluyera
While developing a new concept for a 3-D printed surgical needle, Associate Professor of Mechanical Engineering Parsaoran Hutapea and PhD candidate Mohammad Sahlabadi found an unusual muse: honeybees.
“I told [Mohammad] we should try to look at nature, such as mosquitos, honeybees, wasps, etc.,” said Hutapea, who’s been using 3-D printing technology to develop surgical needles since 2011 with the support of a Department of Defense grant. “We brought some honeybees into the lab, and took out and inspected their stingers using a microscope. The way honeybees sting human skin is very attractive for what we’re trying to develop, because, due mainly to the stinger’s barbs, it goes relatively smoothly straight through the skin and into the tissue.”
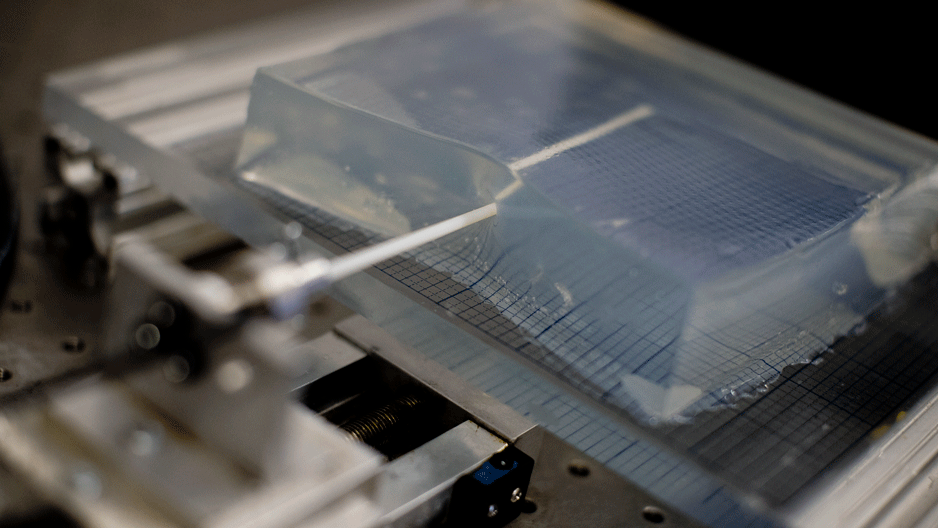
A 3-D printed needle is inserted into gel that simulates human tissue so researchers can measure its accuracy and trajectory. (PHOTO: Ryan S. Brandenberg)
In developing the surgical needles, made from a blend of polymers, Hutapea and Sahlabadi hope to create instruments that can decrease tissue damage while increasing precision. Using the bees’ stingers as inspiration, they devised a design with small barbs (notches) carved into the needle. The notches, Sahlabadi explained, decrease the needles’ insertion and extraction forces, helping to further minimize damage to tissue.
“Generally, a surgical needle will curve due to its tip design when inserted into tissue. The needle deviates from its planned path on the way to the target, such as a cancerous tissue or tumor. With this shape, the curve is limited—it makes it easier to control in a robotics setting,” Hutapea said. “It’s critical, because if the needle curves, you miss the target.”
The needles Hutapea and Sahlabadi developed were also on display last year at the Franklin Institute as part of a temporary 3-D printing exhibit. The pair have also published articles on their needle design, including in the journals Minimally Invasive Therapy and Allied Technologies and Bioinspiration & Biomimetics.
The 3-D-printed needles aren’t yet usable in practice, Hutapea explained, as the needles and 3-D printing technology itself (especially for metal needles with submillimeter size and high aspect ratio—small and long) are still being developed. Eventually, he said, the goal is to develop similar needles usable in practice and have them approved by the Food and Drug Administration so that they can be used to improve minimally invasive surgical procedures.
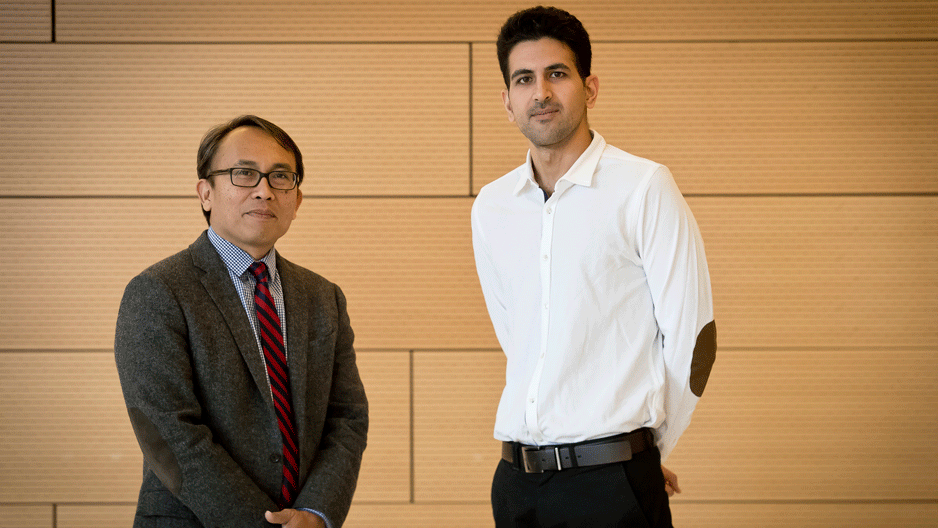
Associate Professor Parsaoran Hutapea, left, and PhD candidate Mohammad Sahlabadi have published several articles on the 3-D printed needles they developed using honeybee stingers for inspiration. (PHOTO: Ryan S. Brandenberg)
“The big question is whether we can manufacture 3-D printed metal needles, and that technology is not here yet. In the meantime, we are currently developing a compromise by looking at a manufacturing method to develop a hybrid metal-polymer needle,” Hutapea explained. “The hope is that in two to three years, we have that technology.”